如何提升UV真空镀膜工艺的良品率?
通常情况下,按照正常的UV真空电镀工艺流程投入1000pcs素材进行真空电镀加工,工艺完成后,最终得到的符合品质要求的电镀良品数量是很难达到1000pcs投入数量的,投入素材的数量与所得良品数量的差,即为真空电镀工艺的制程损耗,制程损耗主要由以下几个方面组成;
1.首件损耗;真空电镀各工序量产前必须要做首件检查,包括外观、颜色、光泽、信赖性、试配组装检查等,检查合格时品管人员签发首件样品开启量产模式,首件检查不合格时,技术人员需要重新调试首件样品并提交品质人员确认,直致首件确认OK后方可以进行批量化生产;UV真空电镀加工工艺按基本的底漆、镀膜、喷面漆三个工序来算,每个工序都要进行首件确认及测试检查,每次首件检查平均需要耗费掉至少5-10pcs的产品,在首件制作一次合格的情况下,各工序首件损耗至少需要15-30pcs产品;
2.制程抽检测试损耗;量产开始后,为监控自动线产品的质量状况,品管人员每隔一段时间就要对下线的产品进行外观检查和附着力等信赖性测试检查,这种检查模式在工厂管理体系中叫做制程跟线巡查,每次跟线巡查大概需要耗费至少3-5pcs的产品做信赖性验证检测,这些做过信赖性检测破坏的产品无法通过返修变为良品,直接做报废处理;若品管巡线检查频率按十分钟检查一次来计算,则一小时的巡查测试次数为六次,巡查测试的产品损耗为18-30pcs;
3.掉线损耗;产品在真空电镀量产过程中,如果夹具与产品组装不紧,很容易造成产品掉线损坏的现象发生;这种掉线损耗往往发生在喷底漆、镀膜、喷面漆的过程中,数量也无法预知;
4.转工序碰划伤损耗:产品在上下线、转工序等有人员参与操作的过程中,会由于人员的操作熟练度、操作手法等因素造成产品与设备、产品与产品之间发生碰擦,造成产品的外观不良;
5.外观不良损耗;产品完成电镀下线后,需要进行100%外观检查再包装出货,所有超出客户外观标准要求的有瑕疵的产品均会被全检品管人员做为不良品剔除,因UV真空电镀工艺的特殊性,这些外观不合格的电镀成品最终无法经过返修或返工变成良品,均需全数做报废处理,这是真空电镀工序损耗的主要组成部分;
综上分析,造成素材损耗的1、2项原因为品质检查测试损耗,这部分损耗必须存在且无法省掉;因此,改善和提升真空镀膜制程良品率的方向就主要集中在后面三个因素上面,常规对策建议如下:
1.掉线改善:夹具设计过程中充分考虑制程过程的各种工况,保证夹具与产品匹配的夹紧力度既不松动也不过紧,杜绝产品在过程中掉落损耗;培训员工装配夹具的手法,装配完成后自检一遍确认装配到位方可上线投产;
2.碰划伤改善:培训员工操作手法,培训完成后管理人员现场应现场验证确认员工的操作效果,确保所有人员均按章操作,避免或尽量减少人为因素造成的产品损坏;
3.外观不良改善:根据真空电镀成品的品管全检报表,可以获知任意一款产品制程不良的前三大类别,通常为颗粒、尘点、毛丝等缺陷居多,加强环境的无尘管控,做好产品上线前的除尘可以有效改善颗粒尘点等不良。
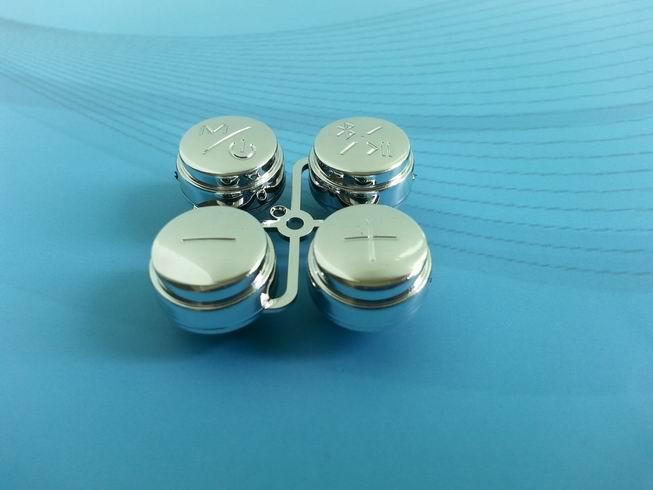